Join Our Team.
There has never been a more exciting time at Rani Therapeutics. We have successfully tested the RaniPill in humans, and we are working towards the ultimate goal of making the oral delivery of biologics a reality for millions of patients. We are growing rapidly and we are actively hiring.
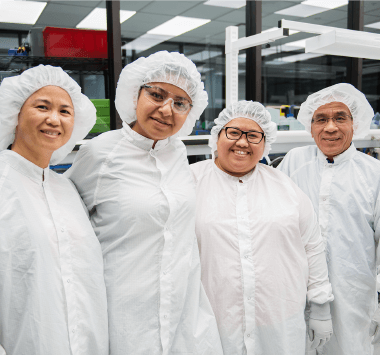
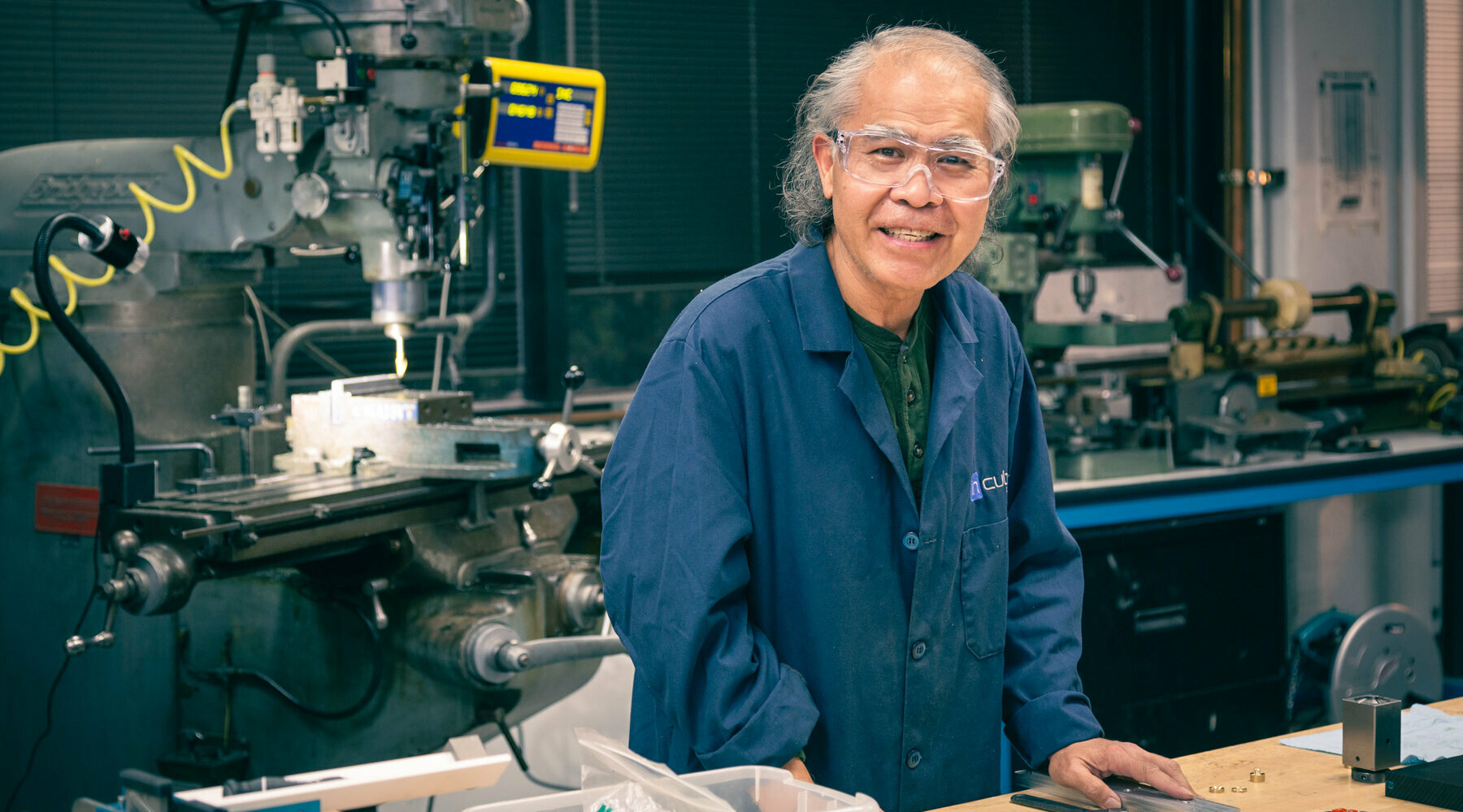
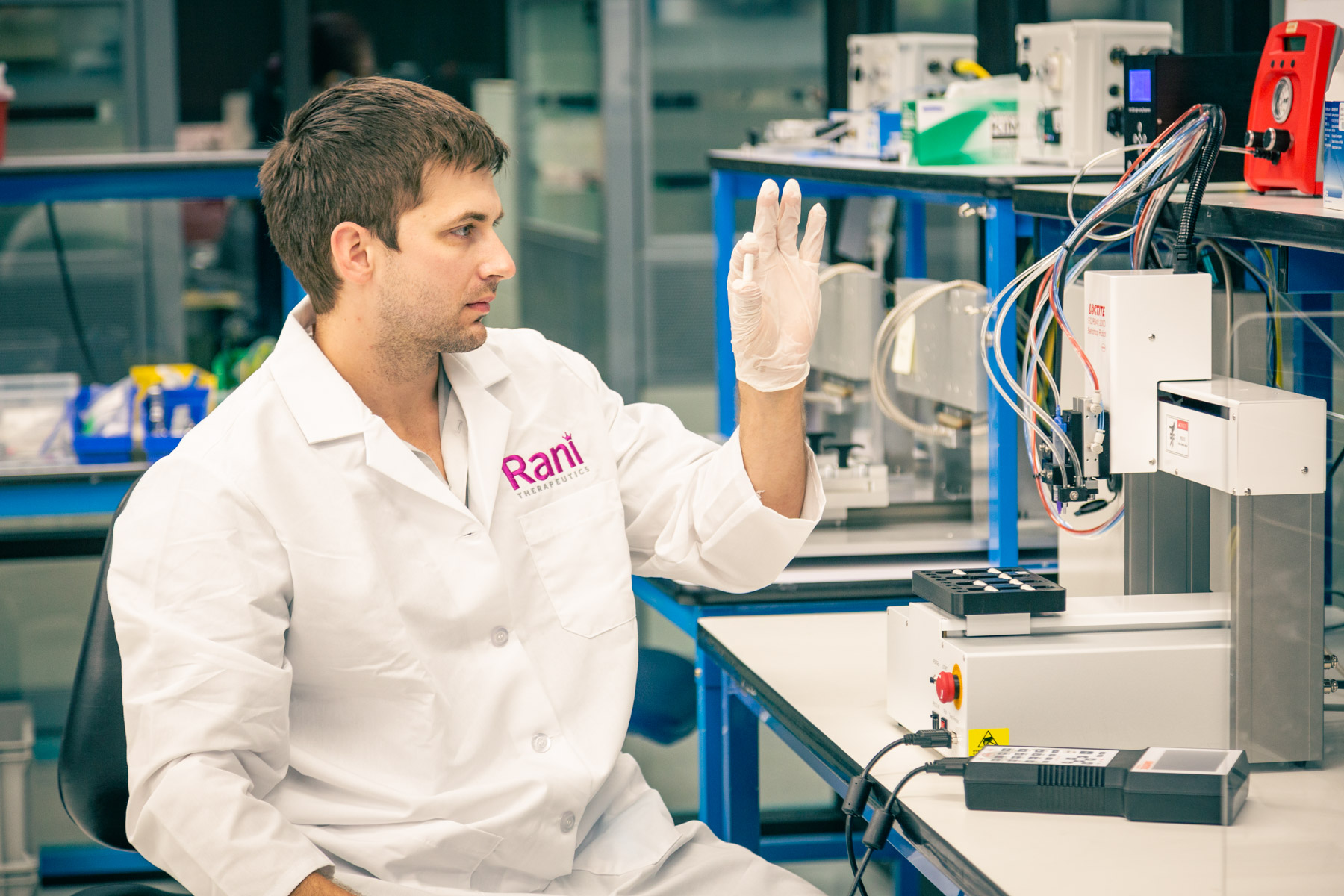

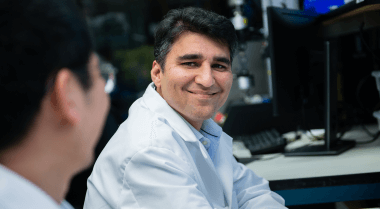
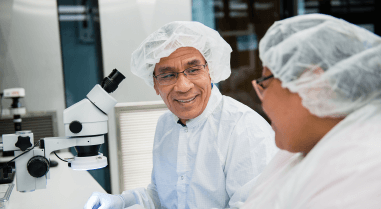
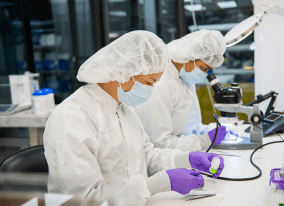
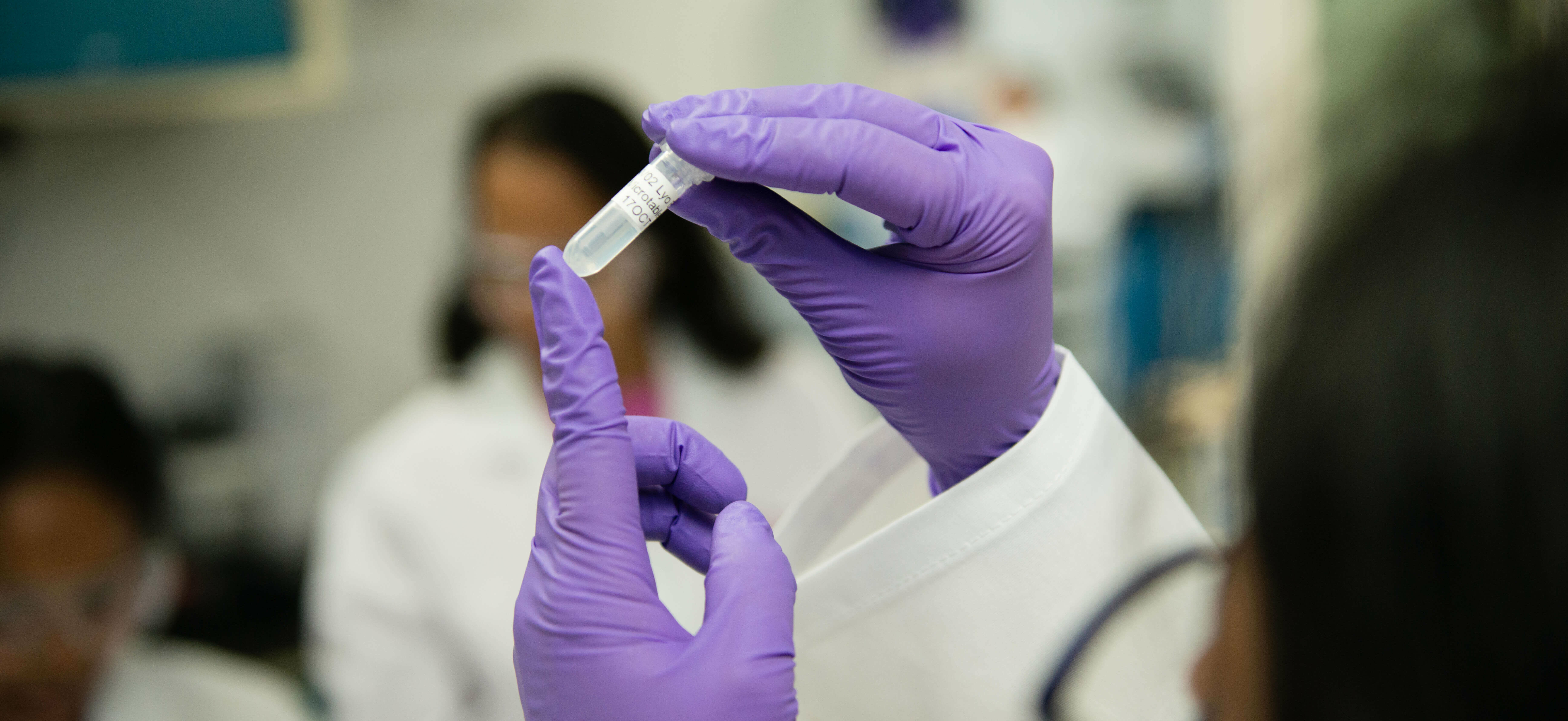
Current Openings.
We are actively hiring and building our team. Check out some of our current open positions. If you think you have the right experience, and would like to be part of a dynamic team, we want to hear from you.